通過(guò)式高壓噴淋清洗機(jī)印制板上殘留物的形成原因和解決的方法。
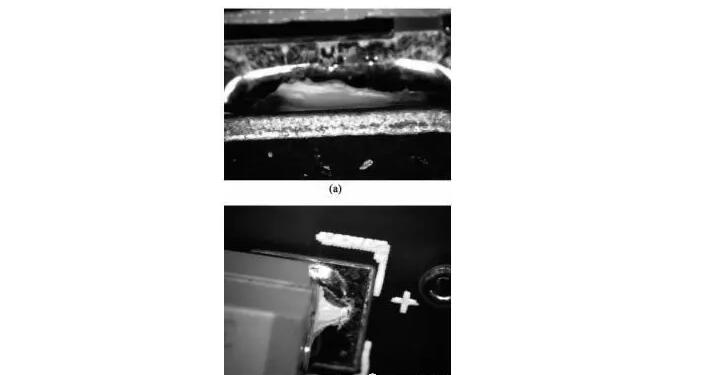
印刷電路板組裝在使用清洗機(jī)清洗后,部分 PCBA 留有許多白色殘?jiān)?,這些殘?jiān)稍S多的化學(xué)物質(zhì)反應(yīng)而成。免清洗助焊劑、免清洗錫膏、電路板上的殘留環(huán)氧樹脂和其他樹脂、元器件的材料和其他一些污染物都對(duì)這些復(fù)雜的化學(xué)反應(yīng)有所貢獻(xiàn)。
關(guān)鍵詞:清洗劑濃度變化 水基清洗劑、 白色粉末、清洗機(jī)、清洗
隨著產(chǎn)品產(chǎn)量的提升,以及對(duì)可靠性要求的提高,引入了噴淋式清洗機(jī),減少手工清洗,提升對(duì)印制板的清洗效率。在使用初期,在清洗器件少、密集程度不高的 PCBA(印制電路板經(jīng)過(guò) SMT 上件,再經(jīng)過(guò) DIP 插件的整個(gè)過(guò)程,簡(jiǎn)稱 PCBA)時(shí),噴淋式水清洗機(jī)表現(xiàn)優(yōu)秀,高效率地完成了清洗任務(wù);但當(dāng)清洗 SMT 器件密集程度較高的 PCBA 時(shí),器件引腳,特別是 IC 引腳間出現(xiàn)了白色粉末狀的物質(zhì),如圖 1 所示。這些白色粉末不僅影響產(chǎn)品外觀,同時(shí)白色粉末外觀表現(xiàn)為疏松的物質(zhì),極易吸收空氣當(dāng)中的潮氣和各種腐蝕性氣體,特別在沿海一帶高鹽霧的地區(qū),有可能對(duì)電路板長(zhǎng)期工作的可靠性造成嚴(yán)重影響。而且,未去除的白色殘?jiān)鼘⒂绊懞笃谕糠笕缛榔岬母街?,影響三防漆的防護(hù)效果和長(zhǎng)期使用壽命。因此,在清洗機(jī)清洗后仍需要人工使用防靜電刷對(duì)白色粉末進(jìn)行清潔,不僅未提升PCBA 的清洗效率,反而增加生產(chǎn)的工作量。
白色粉末形成的機(jī)理
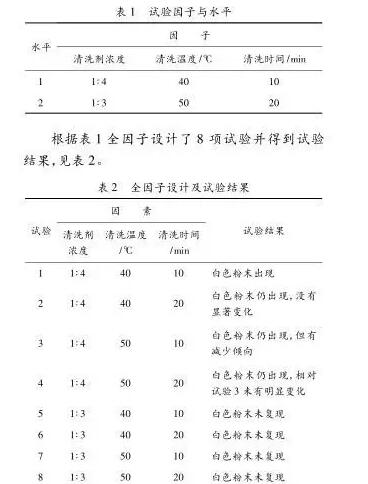
圖1、清洗后引腳出現(xiàn)白色粉末狀物質(zhì)
1.1 采用酒精溶劑手工清洗 PCBA
在未采用水基型溶劑與清洗機(jī)搭配的方式清洗 PCBA 之前,一直采用酒精溶劑手工清洗 PCBA。為驗(yàn)證白色粉末的形成原因及機(jī)理,進(jìn)行以下試驗(yàn)。
將 PCBA 浸泡在酒精溶劑中 30 min,再使用防靜電刷進(jìn)行清潔。此次試驗(yàn)在 PCBA 浸泡后未馬上使用防靜電刷進(jìn)行清潔,而是直接晾干。發(fā)現(xiàn)浸泡后的 PCBA,在直插器件和 SMD 器件引腳均出現(xiàn)了白色粉末。說(shuō)明白色粉末的形成與清洗方式、清洗劑的更換無(wú)關(guān)。為驗(yàn)證白色粉末的成分,將白色粉末委外進(jìn)行紅外光譜分析,發(fā)現(xiàn)白色粉末的主要成分為松香。驗(yàn)證了白色粉末為錫膏焊接、錫絲焊接后助焊劑殘留物。
1.2 白色粉末的形成原因
SMT 生產(chǎn)所使用的錫膏為免清洗錫膏,THT 焊接所使用的焊錫絲為免清洗焊錫絲,而使用的助焊劑 RF800 為松香型免清洗助焊劑。以上材料中所包含的助焊劑均含有松香。
因白色粉末多出現(xiàn)在 IC(貼裝芯片)引腳間,下面詳細(xì)介紹一下回流焊焊接過(guò)程。
SMT 是 SMD 器件(表面貼裝器件)安裝在印制電路板的表面,通過(guò)回流焊的方式加以焊接組裝的電路裝連技術(shù)?;亓骱负附影?4 個(gè)部分:預(yù)熱區(qū)、恒溫區(qū)(活性區(qū))、回流區(qū)、冷卻區(qū)。恒溫區(qū)有兩個(gè)作用,其中之一就是焊錫膏中的助焊劑開始發(fā)生活性反應(yīng),清除焊接表面的氧化物和雜質(zhì),增加焊件表面潤(rùn)濕性能及表面能,使熔化的焊錫能夠很好地潤(rùn)濕焊件表面。在回流區(qū)時(shí)助焊劑附著在焊接表面,促進(jìn)焊錫潤(rùn)濕過(guò)程和防止焊接表面的再氧化。在完成回流焊接后,助焊劑以固化的松香的形式黏附在焊接表面,呈半透明的絕緣物質(zhì) 。因SOP、QFP 等 IC 器件引腳間距遠(yuǎn)遠(yuǎn)小于一般的SMD 器件,在回流焊接過(guò)程中助焊劑延伸的面積較少,導(dǎo)致引腳間的助焊劑殘留較一般的 SMD 器件多,且清洗空間較小,所以清洗難度遠(yuǎn)大于一般SMD 器件。在器件焊接后,原有一層透明的膠膜將助焊劑等殘?jiān)o緊包裹,但清洗破壞了這層透明物質(zhì),使得暴露的殘?jiān)噪y溶的白色粉末的形式表現(xiàn)出來(lái)。為避免白色粉末的產(chǎn)生,或者不做任何清洗,或者做徹底清洗,白色粉末的發(fā)生是由不完全清洗造成的。
水清洗的 5 個(gè)要素:水、清洗劑、時(shí)間、溫度、機(jī)械力。清洗機(jī)與水(去離子水)為固定因素,可調(diào)整因素僅有清洗劑、時(shí)間、溫度。清洗機(jī)設(shè)定的參數(shù)有:清洗溫度、清洗時(shí)間、漂洗溫度、漂洗時(shí)間。
綜合水清洗工藝及清洗機(jī)參數(shù),設(shè)計(jì)試驗(yàn)的參數(shù)有:清洗劑、清洗溫度、清洗時(shí)間、漂洗溫度、漂洗時(shí)間。
2 試驗(yàn)設(shè)計(jì)方案及結(jié)果
此次試驗(yàn)設(shè)計(jì),采用 DOE 的全因子試驗(yàn)方法。全因子試驗(yàn)方法是將每一個(gè)因素的不同水平組合做同樣數(shù)目的試驗(yàn)。
根據(jù)清洗劑清洗 PCBA 的原理,漂洗是對(duì)清洗后殘留在 PCBA 表面的清洗溶劑進(jìn)行清除,漂洗對(duì)白色粉末產(chǎn)生的貢獻(xiàn)不大,此次試驗(yàn)因素中不考慮,作為噪音處理。設(shè)計(jì)試驗(yàn)的因子數(shù)為清洗劑濃度、清洗溫度、清洗時(shí)間 3 個(gè)因子。每個(gè)因子選擇兩個(gè)水平,試驗(yàn)數(shù)為 23,即 8 個(gè)試驗(yàn)。試驗(yàn)因子與水平見表 1。根據(jù)清洗劑的活性特點(diǎn),在 40 ~ 50℃活性較高,故試驗(yàn)中設(shè)定清洗溫度最高不超過(guò) 50℃。試驗(yàn) PCBA均為出現(xiàn)白色粉末的同款 PCBA。
3
通過(guò)式高壓噴淋清洗機(jī)PCBA清洗試驗(yàn)結(jié)果與討論
假定白色粉末出現(xiàn)結(jié)果為 0,未出現(xiàn)結(jié)果為 1。清洗劑濃度為 A 因子,清洗溫度為 B 因子,清洗時(shí)間為 C 因子。各因子低水平為 -1,高水平為 +1,則試驗(yàn)結(jié)果見表
3。計(jì)算各因子的平均值。
平均 A(-) = (0 +0 +0 +0) /4=0
平均 A( + ) = (1 +1 +1 +1) /4=1
平均 B(-) = (0 +0 +1 +1) /4=0.5
平均 B( + ) = (1 +1 +1 +1) /4=0.5
平均 C(-) = (0 +1 +0 +1) /4=0.5
平均 C( + ) = (0 +1 +0 +1) /4=0.5
將各因素高水平下的平均值和低水平下的平均值相減,即得各因素對(duì)平均值的影響,
計(jì)算如下:
A 因素的影響 = (平均 A + ) - (平均 A-)=1
B 因素的影響 = (平均 B + ) - (平均 B-)=0
C 因素的影響 = (平均 C + ) - (平均 C-)=0
如果各因素的高水平與低水平平均值的差為0,則此因素對(duì)輸出變量的均值無(wú)影響,否則說(shuō)明其對(duì)輸出變量的均值有影響。
從以上試驗(yàn)數(shù)據(jù)分析可知,清洗劑濃度為白色粉末產(chǎn)生的關(guān)鍵因子。
3.1 通過(guò)式高壓噴淋清洗機(jī)清洗劑濃度變化的驗(yàn)證
清洗機(jī)在設(shè)定之初,為提升清洗劑的利用率,清洗機(jī)被設(shè)定為清洗劑全循環(huán)使用模式,所以清洗劑在剛完成溶液配比時(shí),濃度滿足 1∶ 3,隨著清洗劑的使用,清洗劑濃度在下降,對(duì)剛配比完的溶液及第一次出現(xiàn)白色粉末的溶液進(jìn)行濃度的測(cè)試。
將清洗劑濃度配比調(diào)整到 1∶ 3,對(duì) PCBA 進(jìn)行清洗,測(cè)試清洗劑濃度為 23% ~ 24%。而剛出現(xiàn)白色粉末的溶液中清洗劑的濃度為 16% ~ 18%。再次驗(yàn)證清洗劑與去離子水的配比濃度為 PCBA清洗后產(chǎn)生白色粉末的主因。
3. 2 實(shí)物驗(yàn)證
使用配比為1:3 的溶液、清洗溫度50℃以及合適的清洗時(shí)間,清洗更加復(fù)雜的 PCBA 時(shí)(元件布局更加密集,元器件引腳間距僅 0.5mm),也未再出現(xiàn)白色粉末。如圖 2 所示。
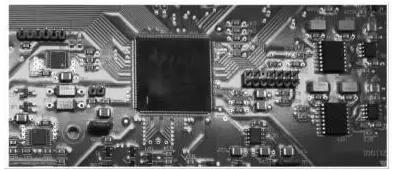
4.通過(guò)式高壓噴淋清洗機(jī)PCBA清洗后白色粉末的形成原因及解決方案結(jié)語(yǔ)
在清洗不同助焊劑殘留物時(shí),清洗劑濃度、清洗時(shí)間、清洗溫度 3 個(gè)因子是影響 PCBA 清洗的主要因子,如更換助焊劑或錫膏種類時(shí),可對(duì)該 3 個(gè)因子進(jìn)行試驗(yàn)設(shè)計(jì),通過(guò)試驗(yàn)設(shè)計(jì)確定最優(yōu)清洗參數(shù)。